Antonio Luca, University of Bremen
|
PhD title: Optimizing the quality of an injection moulded medical micro component via in-line and off-line process monitoring
ESR 8
|
Micro injection moulding processes have to be optimized in order to ensure the required product quality at the micrometre level. A challenging aspect of the process is the achievement of a complete filling of the micro cavity. The process encompasses a large number of parameters (e.g. mould and melt temperatures, injection speed, packing pressure, packing time) to be set properly in order to achieve a good replication of the manufactured part. In this research a medical component with dimensions in the micrometre range and micro features that could lead to a difficult filling of the cavity is investigated by means of micro injection moulding experiments and simulations. Full-factorial designs of experiments and different mould systems are employed in order to improve the part quality after demoulding (e.g. shape accuracy, deformation, roughness, etc.) by characterising the relationship between the machine input parameters, the in-time process parameters and the part quality parameters. In-line and off-line measurements are executed using sensors implemented in the machine and microscopes.
|
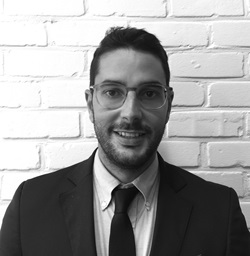
|
Emanuele Cannella, IPU |
PhD title:
High precision tooling for heat assisted micro forging of brittle materials
ESR 12
|
Sintering of metal powder to manufacture small ring-shaped components for a medical instrument application. Literature investigation and research on Electro Current Assisted Sintering (ECAS) processes. Designing and optimising of a tool system for the Electro Sinter Forging application. Tool material selection. Sintering of pure titanium powder to manufacture disk-shape components for experimental tests. Identifying and optimising the main process parameters related to the process. Conducting a fractional factorial design of experiments to highlight the most influencing parameters for a specific output. In-line metrology analysis and identification of -manufacturing fingerprints. Lubricant investigation to optimise the sample ejection after sintering. Numerical simulations for validations of the experimental results. Quality control and test of the sintered components. Analysis of the main mechanical properties, e.g. density, porosity and yield strength of the sintered samples. Geometrical and dimensional tolerance verification
|
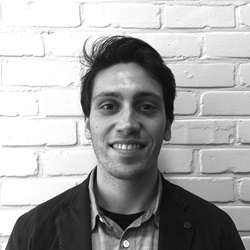 |
Federico Baruffi, DTU
|
PhD title: Integrated micro product/process quality assurance in micro injection moulding production
ESR 1
|
My scientific work focuses on the study and improvement of micro manufacturing processes. I graduated in Mechanical Engineering cum laude at Politecnico di Milano in April 2016, defending a thesis on precision metrology of surface topography developed in collaboration between Technical University of Denmark and LEGO® group. After that, I started a PhD project in May 2016 as early stage researcher (ESR) in the European H2020 project MICROMAN. My MICROMAN PhD project aims at developing and optimizing the micro injection moulding process of an ultra-small three-dimensional micro medical polymeric component. The innovative concept of micro-manufacturing fingerprint is the core of the project: by identifying and linking the most relevant product and process features, the time needed to carry out the quality assurance can be consistently decreased using in-line metrology and process monitoring. The micro injection moulding process can be therefore optimized in-line, resulting in a more accurate and productive manufacturing process.
|

|
Igor Danilov,
Technische Universität Chemnitz |
PhD title:
Micro plasma electrolytic polishing
ESR 6
|
Plasma electrolytic polishing (PeP) is an electrochemical method for surface treatment. During processing, the surface of a workpiece becomes smoother and get higher gloss level. Because of small achievable roughness (Ra < 0.02 μm) and small removal rates, this process can be applied for finishing of precision parts.
In recent years, a lot of studies on PeP have been made. Nevertheless, at presence, only a few research work has been focused on the understanding of the process basics.
Main goals of my study are to develop technology and equipment for PeP of micro parts, to determine process boundaries and to develop multiphysics simulation models of the process that will provide needed understanding of the process.
|
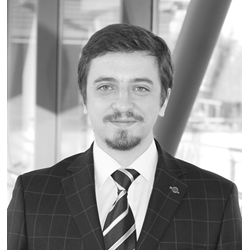 |
Krishna Kumar Saxena,
KU Leuven
|
PhD title: Precision hybrid micro-ECM technology
ESR 4
|
Krishna is working on Precision hybrid micro-ECM technology for his PhD research. He is a part of Micro Precision Engineering group of Mechanical Engineering Department at KU Leuven under the supervision of Prof. Dr. ir Dominiek Reynaerts and Dr. Jun Qian. His research mainly focusses on developing a hybrid process of micro-ECM and pulsed laser for drilling of coated superalloys, exploring the material removal mechanisms under the action of two process energies and evaluation of process fingerprint.
Prior to joining KU Leuven, he has worked as research scholar at University of Auckland, New Zealand and as DAAD scholar at University of Stuttgart, Germany. He holds Master of Technology (Institute gold medalist) from Indian Institute of Technology Gandhinagar. He has also received travel grants to visit Monash University, Australia and ASME IMECE 2014 Canada.
|
 |
Mattia Bellotti,
KU Leuven |
PhD title:
High-efficiency micro-EDM technology
ESR 3
|
Mattia Bellotti is PhD candidate at KU Leuven, Department of Mechanical Engineering, Section of Production engineering, Machine design and Automation, Micro Precision Engineering group. His current research interests are monitoring, control, and optimization of electrical discharge machining (EDM) process at micro scale.
Mattia holds Bachelor’s and Master’s Degrees in Mechanical and Industrial Engineering from Politecnico di Milano. Before joining KU Leuven he has worked as visiting researcher at Brunel University London, where his research has been mainly focused on warpage of thermoplastic parts in extrusion-based additive manufacturing processes.
|
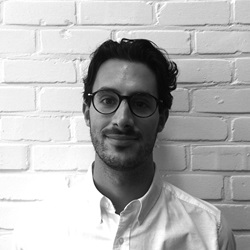 |
Matin Yahyavi Zanjani, Technische Universität Chemnitz |
PhD title:
Micro Electro-Chemical Machining
ESR 5
|
The fundamental principle of all electrochemical machining processes is an anodic dissolution of metallic work pieces under the influence of electric charge transport. The dissolution takes place at the interface between the work piece surface and a liquid ion conductor, called electrolyte.
In Jet-ECM an electrolyte jet supplies direct electric current between the anodic work piece and the cathodic tool.
My Master thesis was on Electrochemical Jet Turing. During the time, as a member of a team, I constructed a jet turning machine which was capable of machining complicated structures, even non-circular by using electrolytic jet. After graduation, I joined a company active in the field of Electrochemical Machining called ECM Technologies B.V. In 2016, I applied for the position on Jet Electrochemical machining at TU Chemnitz and was admitted. I joined the program in September 2016. The main focus of the project is to implement the process and product fingerprint concepts in Micro Jet Electrochemical Machining as well as the integration of an in-line measurement system. Until now, a laser triangulation systems has been integrated to the university Jet electrochemical prototype and some experiments have been done. On the other side, the fingerprints study and experiments are ongoing.
|
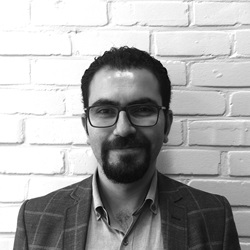 |
Mert Gulcur, University of Bradford |
PhD title:
New technologies and process fingerprinting for optimised production of thermoplastic microneedle arrays
ESR 13
|
Mert Gulcur obtained a BSc degree in Materials Science and Engineering from Gebze Technical University in 2011. He obtained a full scholarship from German Academic Exchange Service (DAAD) and Turkish Education Foundation (TEV) in late 2013 to carry out MSc studies at Karlsruhe Institute of Technology (KIT) on Optics and Photonics with a focus on photovoltaics. After finishing the MSc programme in 2016, he started to work as an early stage researcher in the H2020 - European Innovative Training Network MICROMAN - “Process Fingerprint for Zero-defect Net-shape MICROMANufacturing”.
In this PhD project, the overall optimization of the micro injection moulding process will be achieved by innovative approaches based on: (1) implementation of a process-sensitive and representative finger print feature into the micro moulded application product design to make the product inspection efficient with less inspection effort; (2) establishment of the relation between the micro moulded product quality parameters, the finger print quality response and the micro injection moulding processing conditions; (3) implementation of a real-time inspection tool in the micro injection moulding equipment using both microscopy and moulding parameters monitoring. With these approaches, a fast and robust optimization of micro injection moulding process of the micro moulded microneedle arrays will be achieved.
|
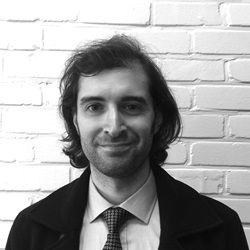 |
Pablo Fook, University of Bremen |
PhD title:
Micro grinding of Dental Ceramic Implants
ESR 7
|
The knowledge about ductile-mode grinding enables the manufacturing of products made of hard and brittle materials with high shape and surface quality. This can be exemplified by the recent production of dental ceramic implants as replacement of the conventional metal implants. Therefore, micro grinding is a key technology for precision micro manufacturing. Nevertheless, further investigations are required on the process metrology and material integrity to improve the quality of the workpieces as well as to reduce the amount of rejected and failed parts.
In this research, the process fingerprint for micro grinding is based on the measurement of relevant process parameters during and after micro grinding of dental ceramic workpieces in order to choose suitable process configurations and improve workpiece features such as material integrity and product design. The fingerprint concept includes in-situ metrology of workpiece and grinding tool, monitoring of process factors, such as vibration, grinding forces and acoustic emission as well as off-line metrology, like mechanical tests and imaging techniques to investigate product integrity in reference to the surface and sub-surface layer characteristics.
|
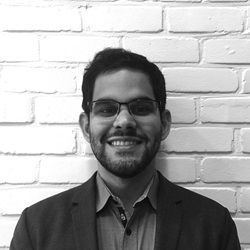 |
Sandeep Kuriakose, Politecnico di Milano |
PhD title: Integrated micro product/process quality assurance in micro extrusion production
ESR 10
|
I am a micro manufacturing enthusiast who is currently working in Micro extrusion area in MICROMAN project group. The recent advancements and researches in extrusion suggest that metal polymer feedstock extrusion can be used as a feasible technology for the production of metal tubes with more advanced properties. Production of multi-lumen micro tubes for assisted fertilization or multi drug delivery is such an application where micro extrusion of feedstock can be distinctively used. Aim of this research work under Microman Marie Curie project is to fabricate micro bi-lumen tubes for assisted fertilization by extrusion of feedstock. Before joining in Microman group, I was working in micro machining of high strength materials using nontraditional machining. My post graduate project titled ‘Machinability study of metallic glass by micro hole drilling using micro-USM and micro-EDM’ provided me with hands on expertise on properties of new high strength materials, processing and tool designing in regards to nontraditional machining especially with Micro-USM and Micro-EDM. Research experience in machining of metallic glass, which has a potential to be used as a bio degradable implants was a motivating factor and very helpful for me to advance in this bio medical device manufacturing field. |
 |
Soufian Benachour, DTU |
PhD title: Development and validation of an intelligent monitoring for micro polishing
ESR 2
|
The PhD project aims at filling the gap related to the efficient polishing of micro forging dies by developing and validating process and related equipment for automated polishing of micro forging dies. Polishing is currently considered as one of the most effective approaches to achieve a smooth surface. It is typically the very last step of a manufacturing process chain. Complex geometries can not be polished efficiently by craftsman, resulting in non-conformities which has a great impact on the total manufacturing cost. For this reason, an improvement in automation that leads to an improvement of repeatability is strongly needed. |
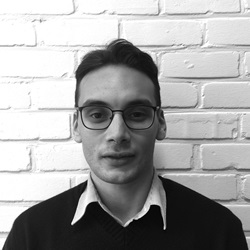 |
Teguh Santoso, University of Nottingham
|
PhD title: Microscale form and surface texture in-situ/in-line small sensor
ESR 11
|
Teguh Santoso received his BEng in Mechanical Engineering and Meng in Manufacturing Engineering in 2010 and 2014, respectively, from University of Indonesia (Indonesia). Since 2016, he has joined the MICROMAN Project and conducting research about in-line metrology.
The research background: Advances in production technologies demand fast and accurate in-line metrology so that part inspection does not become a bottle-neck in the manufacturing process chain. However, many manufacturing industries still do not implement in-line metrology due to lack of available methods that can be conveniently adapted to their production systems. In-line metrology measures appropriate parameters immediately after the associated process step is finished. Therefore, modern production technology efficiency can be improved both in traditional and smart factories (Industry 4.0).
The PhD project aims to develop a fast and accurate non-contact optical in-line metrology module for form and surface texture. Many aspects of precision design will be applied in the development of the module. In addition, calibration methods and a performance verification infrastructure will be developed to ensure the optical instrument’s traceability. Furthermore, the module will utilise smartphone-like electronics borrowed from the mobile phone industry that also incorporate wireless LAN features to ease integration and communication.
|
 |
Yukui Cai, University of Strathclyde |
PHD title:
Ultra precision flexible microforming of surgical tools
ESR 9
|
The superhydrophobic surface shows high resistance to bacterial contamination. With the increase of contact angle, the number of bacteria decreased. Therefore, manufacturing superhydrophobic surface can be the first step in achieving antimicrobial function. There are various approaches for the preparation of superhydrophobic structures. Laser cutting approach is a contactless and especially effective machining approach to manufacturingmicro structures on variety of materials. Until now, my scientific work major focus on manufacturing of hydrophobic structures on medical stainless steel 316L, which is widely used on medical instrument. a fiber laser with 100 ns pulse duration was used to fabricate micro structures on 316L stainless steel. The experimental surface have a high contact angle of 153°and a small sliding angle about 4°.
From this research, my practical skills related with laser machining and CNC was improved. Currently, my research focus on learn the Programming language (Fortran) and smoothed-particle hydrodynamics (SPH) computational method.
|
 |